Styrene butadiene rubber
Styrene-Butadiene Rubber (SBR) stands as a widely utilized synthetic rubber, created through the polymerization of styrene and butadiene monomers. This copolymerization process results in a versatile elastomer, combining the beneficial properties of both constituent monomers. SBR is produced through emulsion or solution polymerization methods, allowing for customization to meet specific application requirements.
This cost-effective and widely available synthetic rubber finds applications across diverse industries due to its balanced combination of resilience, flexibility, and durability. In tire manufacturing, SBR is a key component, contributing to both tire treads and sidewalls. Its excellent abrasion resistance ensures prolonged tire life and reliable performance on various road surfaces. The flexibility and resilience of SBR also make it a preferred choice for footwear, with applications extending to shoe soles and various footwear components.
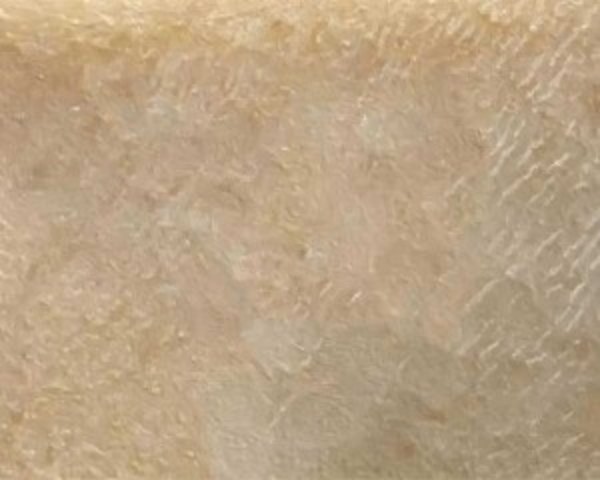
Functions and Characteristics
- Cost-Effectiveness: SBR is renowned for its cost-effectiveness, making it a preferred choice in applications where a balance between performance and affordability is crucial.
- Versatility: The copolymerization of styrene and butadiene imparts a wide range of properties to SBR, allowing its use in diverse applications across industries.
- Tensile Strength: SBR displays excellent tensile strength, providing durability and strength in applications where mechanical performance is crucial.
- Abrasion Resistance: The material demonstrates good abrasion resistance, particularly valuable in tire manufacturing for tire treads and sidewalls.
- Flexibility: SBR maintains flexibility even in lower temperatures, contributing to its versatility in various weather conditions.
- Adhesion Properties: SBR possesses good adhesion properties, making it valuable in the formulation of adhesives and sealants. It contributes to the bonding strength and sealing capabilities of the final products.
- Water Resistance: SBR exhibits resistance to water, making it suitable for applications in damp or wet environments, such as construction materials and industrial belts.
- Resilience: The resilience of SBR makes it ideal for applications where the material undergoes repeated stress or deformation, contributing to its longevity in various settings.
Specifications:
Property/Unit | Specification | Test Method |
Appearance | Meet the requirements | Visual |
Volatile matter content (%) ≤ | 0.21 | GB/T 24131-2009, hot-mill method |
Ash content (%) ≤ | 0.04 | GB/T 4498. 1-2013, method A |
Organic-acid content (%) | 5.96 | GB/T 8657-2014, method B |
Soap content (%) ≤ | 0.04 | GB/T 8657-2014, method B |
Bound styrene content (%) | 23.6 | GB/T 8658-1998 |
Mooney Viscosity (Raw Rubber), ML (1+4) 100 °C | 51-52 | GB/T 1232. 1 – 2016 |
Mooney Viscosity (Compound Rubber), ML (1+4) 100 °C ≤ | 76 | GB/T 1232. 1 -2016 (ASTM IRB
No.8) |
Modulus at 300% (145°C, 35 min) (MPa) | 18.0 | GB/T 8656-2018 formulation 2B
(ASTM IRB No.8), GB/T 528-2009 (Type 1 cutters) |
Tensile Strength (145°C, 35 min) (MPa) ≥ | 27.0 | |
Elongation at break (145°C, 35 min) (%) ≥ | 420 |
Major Applications
Industrial Belting:
SBR's strength and flexibility make it suitable for industrial belts, providing reliable performance in material handling processes such as conveyors.
Consumer Goods Manufacturing:
SBR finds applications in the production of conveyor belts, hoses, and coated fabrics used in various consumer goods, benefiting from its mechanical strength and cost-effectiveness.
-
Product Package
Rubber is wrapped with PE film (thickness:0.046mm~0.054mm,melting point≤110℃). Package outside is a separate paper-plastic bag (a piece of rubber, 35kg) or a big PE bag (36 pieces of rubber, 1.26MT).
-
Storage and transportation
Optimum storage temperature is 10℃~35℃, storage warehouse should keep dry and keep away from sunshine. Storage condition reference GB/T 19188 (ISO 7664, IDT). The storage period is 12 months.
In Needs of Rubber Vulcanization Accelerators Solution?
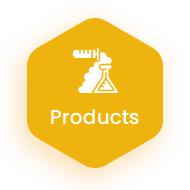