CBS Rubber: Properties, Applications, and Benefits
19/01/2024
CBS rubber is a type of synthetic rubber that has been widely used in various industries. The name “CBS” stands for N-cyclohexyl-2-benzothiazolesulfenamide, which is the chemical name of the compound. This rubber is known for its excellent resistance to abrasion, tearing, and cracking, making it a popular choice for applications that require durability and strength.
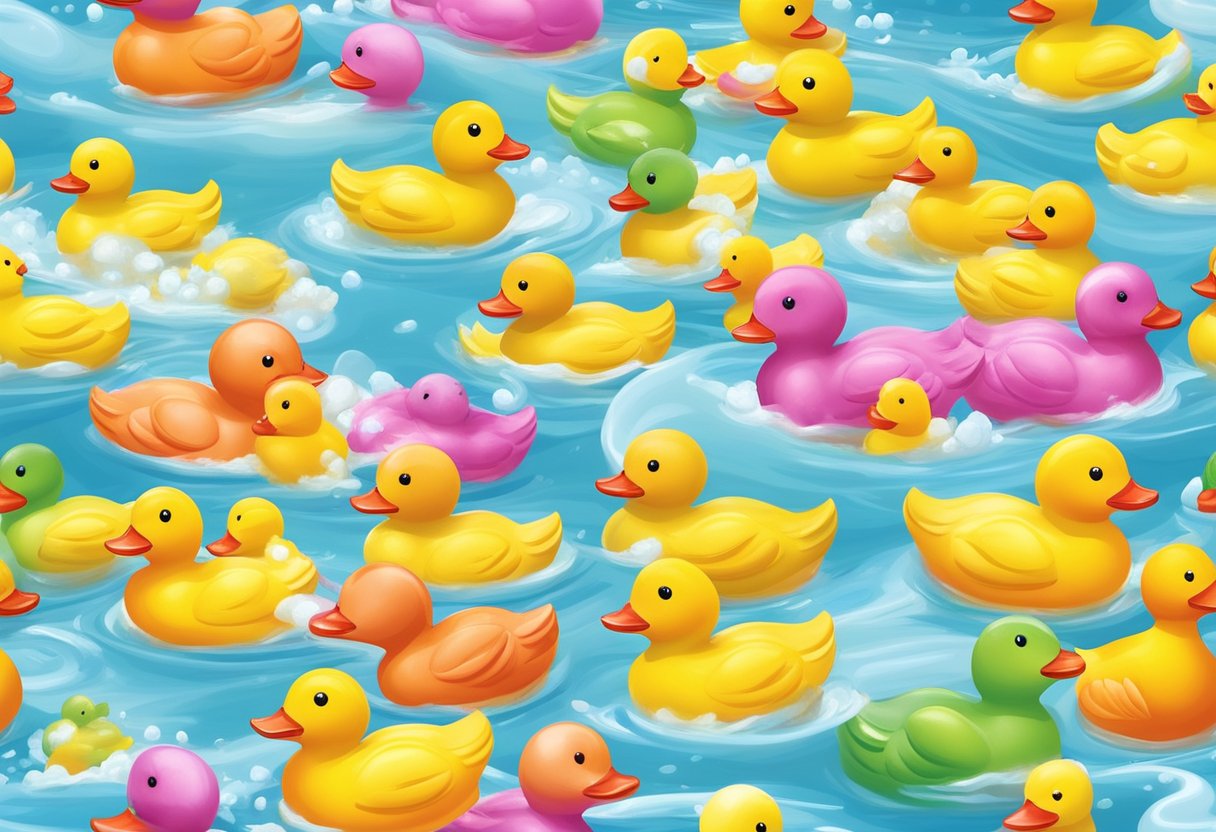
CBS rubber was first developed in the 1930s and has since become a staple in the rubber industry. It is commonly used in the production of tires, conveyor belts, and other industrial products that require high performance and durability. The unique properties of CBS rubber make it ideal for applications that involve heavy loads, high speeds, and harsh environments.
In recent years, CBS rubber has also been used in the production of consumer goods such as footwear and sporting equipment. Its excellent resistance to wear and tear make it a popular choice for products that are subjected to frequent use and abuse. Overall, CBS rubber is a versatile material that has played an important role in the development of modern industry and continues to be an essential component in many products today.
Chemical Composition of CBS Rubber
CBS rubber, also known as N-cyclohexyl-2-benzothiazolesulfenamide, is a type of synthetic rubber widely used in the tire industry due to its excellent properties such as high elasticity, durability, and resistance to abrasion. The chemical composition of CBS rubber plays a crucial role in determining its properties and performance.
Sulfur Content
Sulfur is a key component of CBS rubber and is added during the vulcanization process to crosslink the polymer chains and improve the mechanical properties of the rubber. The sulfur content in CBS rubber typically ranges from 1.5% to 2.5% by weight. However, excessive sulfur content can lead to brittleness and reduced elasticity, while insufficient sulfur content can result in poor vulcanization and reduced durability.
Accelerators and Activators
Apart from sulfur, CBS rubber also contains accelerators and activators that help to speed up the vulcanization process and improve the properties of the rubber. Common accelerators used in CBS rubber include mercaptobenzothiazole (MBT) and diphenylguanidine (DPG), while activators such as zinc oxide and stearic acid are also added to enhance the curing process.
It is worth noting that the type and amount of accelerators and activators used in CBS rubber can significantly affect its properties. For example, excessive use of MBT can lead to scorching and reduced aging resistance, while insufficient use of zinc oxide can result in poor adhesion and reduced tensile strength.
In summary, the chemical composition of CBS rubber is a complex mixture of sulfur, accelerators, and activators that determines its properties and performance. A balanced composition of these components is essential to ensure the optimal performance of CBS rubber in various applications.
Manufacturing Process of CBS Rubber
CBS rubber is a type of synthetic rubber that is widely used in the production of tires, belts, hoses, and other industrial products. The manufacturing process of CBS rubber involves several steps, including mixing procedures and vulcanization.
Mixing Procedures
The first step in the manufacturing process of CBS rubber is mixing the raw materials. The raw materials used in the production of CBS rubber include butadiene, styrene, and acrylonitrile. These raw materials are mixed in a reactor vessel under controlled conditions of temperature and pressure.
The mixing process involves the polymerization of the raw materials to form a polymer. The polymer is then dissolved in a solvent to form a rubber solution. The rubber solution is then filtered to remove any impurities.
Vulcanization
The next step in the manufacturing process of CBS rubber is vulcanization. Vulcanization is a process in which the rubber is heated with sulfur to improve its strength, durability, and elasticity. The vulcanization process involves heating the rubber to a temperature of around 150°C in the presence of sulfur.
During the vulcanization process, the sulfur reacts with the rubber to form cross-links between the polymer chains. These cross-links improve the strength and durability of the rubber. The vulcanized rubber is then cooled and cut into the desired shape.
In conclusion, the manufacturing process of CBS rubber involves several steps, including mixing procedures and vulcanization. The process is carefully controlled to ensure the quality and consistency of the final product. CBS rubber is a versatile synthetic rubber that is widely used in the production of industrial products.
Properties of CBS Rubber
Physical Properties
CBS rubber, also known as N-cyclohexyl-2-benzothiazolesulfenamide, is a type of synthetic rubber that is widely used in the production of tires, conveyor belts, and other rubber products. It is a light yellow powder that is soluble in acetone, benzene, and chloroform, and is insoluble in water.
The density of CBS rubber is approximately 1.31 g/cm³, and its melting point is around 98-100°C. It has a molecular weight of 264.4 g/mol, and its chemical formula is C13H16N2S2.
Mechanical Properties
CBS rubber is known for its excellent mechanical properties, which make it a popular choice for use in the production of rubber products. It has a high tensile strength, good elongation at break, and excellent resistance to abrasion and fatigue.
CBS rubber also has good heat resistance, which allows it to maintain its mechanical properties at high temperatures. It has a low compression set, which means that it can maintain its shape and size even after being compressed for a long period of time.
In addition, CBS rubber has good adhesion to metals and other materials, which makes it a popular choice for use in the production of rubber-metal bonded products.
Overall, the physical and mechanical properties of CBS rubber make it a versatile and reliable material for a wide range of applications in the rubber industry.
Applications of CBS Rubber
CBS rubber, also known as N-cyclohexyl-2-benzothiazolesulfenamide, is a type of rubber accelerator that is widely used in various industries. Its unique properties make it an ideal material for a wide range of applications.
Automotive Industry
In the automotive industry, CBS rubber is commonly used in the production of tires. It acts as an accelerator during the vulcanization process, which helps to improve the strength and durability of the tire. CBS rubber is also used in the production of other rubber components such as hoses, belts, and seals. Its high thermal stability and low volatility make it an excellent choice for these applications.
Consumer Products
CBS rubber is also used in a variety of consumer products. It is commonly found in the production of rubber gloves and other protective clothing. Its excellent resistance to heat and chemicals makes it an ideal material for these applications. CBS rubber is also used in the production of footwear, particularly in the soles of shoes. Its unique properties help to improve the durability and comfort of the shoe.
Overall, CBS rubber is a versatile material that has a wide range of applications in various industries. Its unique properties make it an ideal choice for applications that require high strength, durability, and resistance to heat and chemicals.
Comparison with Other Accelerators
CBS rubber is a popular accelerator used in the rubber industry due to its numerous advantages over other accelerators. Here’s a comparison of CBS with two other popular accelerators:
MBT Accelerators
MBT accelerators are known for their fast curing rates and excellent scorch safety. However, they have a relatively short curing time and are not suitable for high-temperature applications. CBS rubber, on the other hand, offers a longer curing time and better heat resistance, making it ideal for high-temperature applications.
Sulfenamide Accelerators
Sulfenamide accelerators are known for their excellent aging properties and low compression set. However, they have a slow curing rate and are not suitable for low-temperature applications. CBS rubber, on the other hand, offers a faster curing rate and better low-temperature performance, making it ideal for low-temperature applications.
Overall, CBS rubber offers a unique combination of properties that make it an excellent choice for a wide range of rubber applications. Its superior heat resistance, longer curing time, and better low-temperature performance make it a preferred choice over other accelerators in many applications.
Environmental Impact and Safety
Disposal Considerations
CBS rubber is a synthetic rubber that is not biodegradable and can persist in the environment for a long time. Disposal of CBS rubber should be done in accordance with local regulations. It is recommended to recycle CBS rubber whenever possible. If recycling is not possible, CBS rubber should be disposed of in a landfill that is designed to handle non-biodegradable waste.
Handling and Storage
CBS rubber should be handled with care to prevent exposure to skin, eyes, and mucous membranes. When handling CBS rubber, it is recommended to wear gloves, safety glasses, and a dust mask. CBS rubber should be stored in a cool, dry, and well-ventilated area. It should be kept away from heat, flames, and oxidizing agents.
Overall, CBS rubber is considered safe for use in various applications. However, it is important to follow proper handling and disposal procedures to minimize any potential environmental impact and ensure safety.
Regulatory Framework
CBS rubber is a widely used material in various industries. As such, there are regulatory frameworks in place to ensure its safety and compliance with global standards.
Global Standards
CBS rubber is subject to global standards set by various organizations such as the International Organization for Standardization (ISO) and the American Society for Testing and Materials (ASTM). These standards ensure that CBS rubber products meet certain quality, safety, and performance requirements.
For example, ISO 9001 sets the requirements for quality management systems, while ASTM D2000 specifies the properties of rubber materials such as tensile strength and elongation. Compliance with these standards is crucial in ensuring that CBS rubber products are safe and reliable.
Compliance Requirements
In addition to global standards, CBS rubbers is also subject to various compliance requirements set by regulatory bodies such as the Environmental Protection Agency (EPA) and the Occupational Safety and Health Administration (OSHA). These requirements aim to ensure that CBS rubbers production and use do not pose a threat to human health and the environment.
For instance, the EPA regulates the disposal of CBS rubbers waste to prevent pollution, while OSHA sets standards for worker safety in CBS rubbers manufacturing facilities. Compliance with these requirements is necessary to avoid legal and financial penalties and to maintain a good reputation in the industry.
Overall, the regulatory framework for CBS rubbers aims to ensure its safety, quality, and compliance with global standards and regulations. Compliance with these requirements is essential for the success and sustainability of the CBS rubbers industry.
Market Trends for CBS Rubbers
Demand Analysis
The demand for CBS rubbers has been increasing steadily in recent years due to its unique properties and versatility. CBS rubbers is widely used in the production of tires, conveyor belts, hoses, and other industrial products. The growth in the automotive industry and the construction sector has been driving the demand for CBS rubber.
The increasing demand for fuel-efficient vehicles has led to the development of high-performance tires that use rubber as a key component. Rubber provides excellent wear resistance, high grip, and low rolling resistance, making it an ideal material for tire production.
Moreover, the demand for rubber in the construction sector has been increasing due to its excellent weather resistance and durability. Rubber is widely used in the production of roofing materials, sealants, and adhesives.
Supply Chain Dynamics
The supply chain for rubber is complex and involves several stages, including harvesting, processing, and distribution. The main producers of rubber are located in Southeast Asia, particularly in Indonesia, Thailand, and Vietnam.
The production of rubber is heavily reliant on weather conditions, and any adverse weather can significantly impact the supply of rubber. Additionally, the increasing demand for rubber has put pressure on the supply chain, leading to price fluctuations and supply chain disruptions.
To mitigate these risks, several companies are investing in research and development to find alternative materials that can replace rubber. However,rubber remains a popular choice due to its unique properties and versatility.
In conclusion, the demand for rubber is expected to continue to grow in the coming years, driven by the growth in the automotive industry and the construction sector. However, the supply chain for CBS rubber remains vulnerable to weather conditions and supply chain disruptions, which could impact the availability and price of rubber.
Innovations in CBS Rubber Technology
Recent Developments
CBS rubber, also known as N-cyclohexyl-2-benzothiazole sulfenamide, is a widely used accelerator in the rubber industry. Recent developments in rubber technology have focused on improving its performance, safety, and sustainability.
One of the major advancements in rubber technology is the use of nanotechnology to improve its dispersion and compatibility with other rubber chemicals. This has led to better processing and mechanical properties of rubber compounds containing CBS.
Another area of innovation is the development of rubber with reduced toxicity and allergenicity. This has been achieved by modifying the chemical structure of and using safer processing methods. These improvements have made CBS rubber a safer and more sustainable option for the rubber industry.
Future Prospects
The future of rubber technology looks promising with ongoing research and development efforts. One area of focus is the development of rubber with improved aging resistance, which would increase the lifespan of rubber products.
Another area of interest is the use of rubber in combination with other accelerators to improve the performance of rubber compounds. This could lead to the development of more efficient and cost-effective rubber products.
Overall, the innovations in rubber technology are expected to improve the performance, safety, and sustainability of rubber products. As the rubber industry continues to evolve, rubber will remain an important accelerator in the production of high-quality rubber products.
Quality Control and Testing
Rubber takes quality control and testing seriously to ensure that their products meet the highest standards. The company’s quality control team performs various tests to ensure that their products meet the required specifications and are safe to use.
Standard Testing Methods
Rubber uses various testing methods to ensure that their products meet the required specifications. The company uses a combination of physical and chemical tests to determine the quality of their products. Some of the standard testing methods used by the company include:
- Tensile strength test: This test measures the maximum stress that a material can withstand before breaking. Rubber performs this test to determine the strength of their products.
- Compression set test: This test measures the ability of a material to recover its original shape after being compressed. CBS Rubbers performs this test to ensure that their products can withstand compression without losing their shape.
- Hardness test: This test measures the resistance of a material to indentation. CBS Rubbers performs this test to determine the hardness of their products.
Quality Assurance Practices
CBS Rubbers has implemented quality assurance practices to ensure that their products meet the highest standards. The company follows a strict quality assurance process that involves the following steps:
- Raw material inspection: CBS Rubbers inspects all raw materials before using them in their products. The company only uses high-quality raw materials to ensure that their products meet the required specifications.
- In-process inspection: CBS Rubbers performs in-process inspections to ensure that their products are manufactured according to the required specifications.
- Final inspection: CBS Rubbesr performs final inspections on all finished products to ensure that they meet the required specifications and are safe to use.
Overall, CBS Rubber’s quality control and testing practices ensure that their products meet the highest standards and are safe to use.
Challenges and Limitations
Performance Issues
CBS rubbers is known for its excellent performance in terms of heat resistance, abrasion resistance, and aging resistance. However, there are still some performance issues that need to be addressed.
One of the major performance issues with CBS rubbers is its low resistance to oils and solvents. This can limit its use in certain applications where exposure to these substances is common. Additionally, CBS rubbers has a tendency to shrink and crack over time, which can reduce its effectiveness and lifespan.
Economic Constraints
While CBS rubbeS has many desirable properties, it can be expensive to produce and process. This can limit its use in certain industries where cost is a major factor. Additionally, the availability of raw materials used to produce CBS rubber can fluctuate, which can impact pricing and availability.
Another economic constraint is the limited range of colors available in CBS rubberS. This can limit its use in applications where color is an important factor, such as in consumer products or branding.
Overall, while CBS rubberS has many desirable properties, there are still challenges and limitations that need to be addressed in order to fully realize its potential.