C5 Petroleum Resin: Properties, Applications, and Benefits
20/01/2024
C5 petroleum resin is a type of hydrocarbon resin that is commonly used in a variety of industrial applications. It is a byproduct of the petroleum refining process and is produced by the thermal cracking of heavy petroleum feedstocks. C5 petroleum resin is a highly versatile material that offers a wide range of benefits, including excellent adhesion, good thermal stability, and low odor.
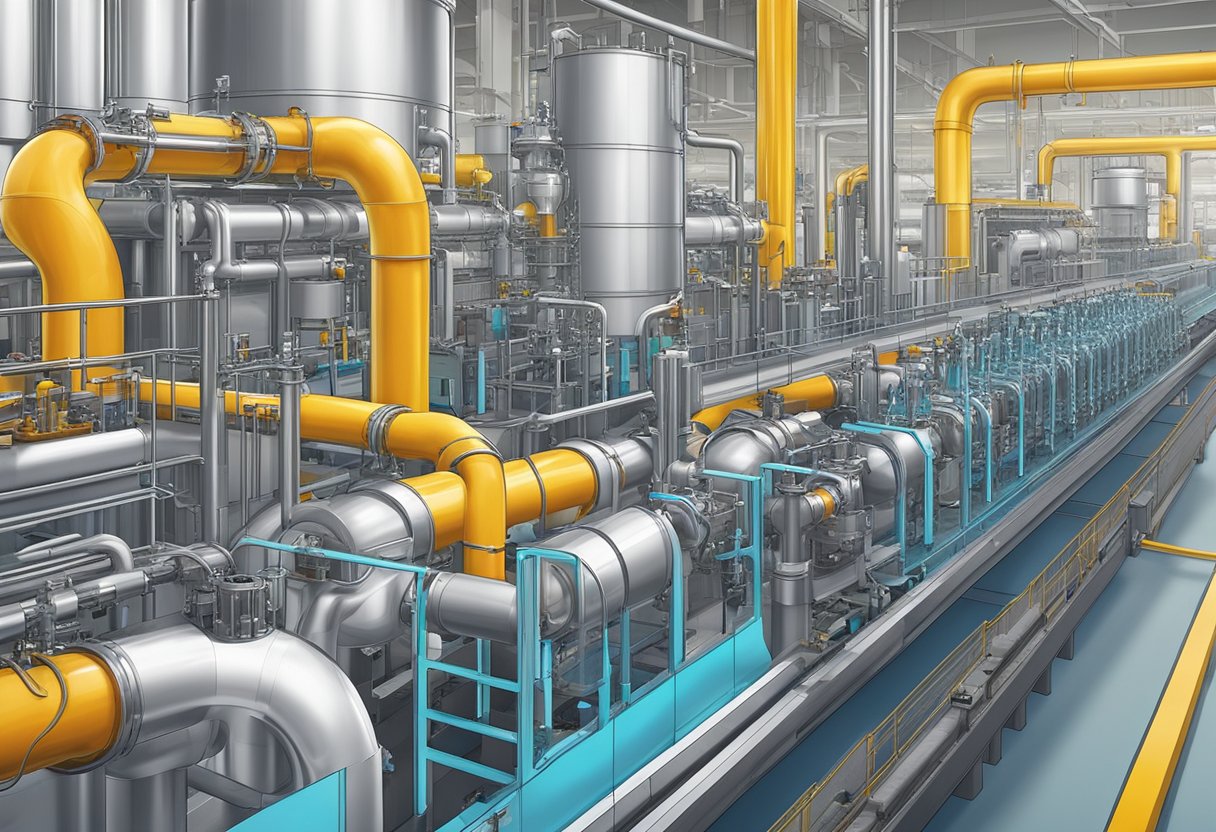
One of the primary uses of C5 petroleum resin is in the production of adhesives and sealants. It is often used as a tackifier, which helps to improve the adhesion properties of the final product. C5 petroleum resin is also used in the production of hot-melt adhesives, which are commonly used in the packaging and labeling industries. In addition to adhesives, C5 petroleum resin is also used in the production of printing inks, coatings, and rubber compounding.
Despite its many benefits, C5 petroleum resin is not without its drawbacks. It is a non-renewable resource and its production can have a negative impact on the environment. However, efforts are being made to develop more sustainable alternatives to C5 petroleum resin, such as bio-based resins. As the demand for environmentally friendly materials continues to grow, it is likely that we will see a shift away from traditional petroleum-based resins towards more sustainable options.
Chemical Composition of C5 Petroleum Resin
C5 petroleum resin is a thermoplastic resin derived from the polymerization of C5 fraction of petroleum. It is a low molecular weight resin with a softening point ranging from 80°C to 120°C. The chemical composition of C5 petroleum resin varies depending on the type of feedstock used and the manufacturing process.
C5 petroleum resin consists primarily of aliphatic olefins and diolefins with a minor amount of aromatic hydrocarbons. The resin also contains functional groups such as carboxylic acid, ketone, and hydroxyl groups. The presence of these functional groups contributes to the resin’s excellent adhesion, compatibility, and solubility properties.
The table below shows the typical chemical composition of C5 petroleum resin:
Component | Typical Range |
Aliphatic olefins | 40-60% |
Diolefins | 30-50% |
Aromatic hydrocarbons | 5-15% |
Carboxylic acid groups | 0.5-1.5% |
Ketone groups | 0.5-1.5% |
Hydroxyl groups | 0.5-1.5% |
C5 petroleum resin is widely used in various industries such as adhesives, coatings, rubber, and printing inks due to its excellent properties such as tackiness, color stability, and resistance to water and chemicals. The chemical composition of C5 petroleum resin plays a significant role in determining its properties and applications.
Production Process of C5 Petroleum Resin
Feedstock Selection
The production process of C5 petroleum resin involves the selection of appropriate feedstocks. The feedstocks used in the production of C5 petroleum resin are derived from the distillation of crude oil. The feedstocks are selected based on their chemical composition and physical properties. The feedstocks are typically composed of C5 aliphatic olefins, which are obtained from the cracking of naphtha. The feedstocks are selected based on their purity, volatility, and reactivity.
Polymerization Techniques
The polymerization process involves the conversion of the selected feedstocks into C5 petroleum resin. The polymerization process is carried out using various techniques such as solution polymerization, bulk polymerization, and emulsion polymerization. The choice of polymerization technique depends on the desired properties of the final product.
In solution polymerization, the feedstocks are dissolved in a suitable solvent and polymerized using a catalyst. In bulk polymerization, the feedstocks are polymerized in the absence of a solvent. In emulsion polymerization, the feedstocks are polymerized in the presence of an emulsifying agent.
Post-Processing Steps
After the polymerization process, the C5 petroleum resin is subjected to post-processing steps to improve its quality and properties. The post-processing steps include hydrogenation, distillation, and blending.
Hydrogenation involves the addition of hydrogen to the C5 petroleum resin to improve its color, odor, and stability. Distillation is used to separate the C5 petroleum resin into different grades based on their properties. Blending is the final step in the production process, where different grades of C5 petroleum resin are mixed to obtain the desired properties.
In conclusion, the production process of C5 petroleum resin involves the selection of appropriate feedstocks, polymerization using various techniques, and post-processing steps to improve its quality and properties. The final product is a versatile and widely used material in various industries such as adhesives, coatings, and rubber.
Properties and Specifications of C5 Petroleum Resin
C5 Petroleum Resin is a type of thermoplastic resin that is derived from petroleum. It is a versatile material that has a wide range of applications in various industries, including adhesives, coatings, and printing inks. Here are some of the properties and specifications of C5 Petroleum Resin:
- Color: C5 Petroleum Resin is usually yellow or light brown in color, but it can also be produced in other colors depending on the application.
- Softening Point: The softening point of C5 Petroleum Resin is typically between 80°C to 120°C, which makes it suitable for use in hot melt adhesives and other applications that require high temperature resistance.
- Viscosity: The viscosity of C5 Petroleum Resin varies depending on the molecular weight and degree of polymerization. It can range from low to high viscosity, which makes it suitable for various applications such as coatings and inks.
- Compatibility: C5 Petroleum Resin is compatible with a wide range of polymers, including natural and synthetic rubbers, polyethylene, and polypropylene. This makes it an ideal material for use in adhesive formulations and other applications that require good compatibility with other materials.
- Solubility: C5 Petroleum Resin is soluble in a wide range of solvents, including aliphatic and aromatic hydrocarbons, esters, and ketones. This makes it easy to use in various applications such as coatings and inks.
Overall, C5 Petroleum Resin is a versatile material that has a wide range of properties and specifications that make it suitable for various applications in different industries. Its unique properties such as high temperature resistance and good compatibility with other materials make it a popular choice for adhesive formulations, coatings, and printing inks.
Applications of C5 Petroleum Resin
C5 Petroleum Resin is a versatile material with various applications in different industries. Here are some of the most common uses of C5 Petroleum Resin:
Adhesive Industry
C5 Petroleum Resin is widely used in the adhesive industry due to its excellent tack and adhesion properties. It is commonly used in hot-melt adhesives, pressure-sensitive adhesives, and solvent-based adhesives. C5 Petroleum Resin improves the adhesive’s performance and helps to increase its cohesion and adhesion strength.
Rubber Compounding
C5 Petroleum Resin is also used in rubber compounding. It is added to rubber formulations to improve their tackiness, adhesion, and processability. C 5 Petroleum Resin also enhances the durability and weather resistance of rubber products.
Printing Inks
C 5 Petroleum Resin is an essential component of printing inks, especially in the production of flexographic and gravure inks. It is added to the ink formulation to improve its adhesion, viscosity, and gloss. C 5 Petroleum Resin also helps to reduce the drying time of the ink and improve its printability.
Paints and Coatings
C 5 Petroleum Resin is used in the production of paints and coatings. It is added to the formulation to improve the adhesion, hardness, and gloss of the coating. C 5 Petroleum Resin also helps to improve the coating’s resistance to water, chemicals, and UV light.
C 5 Petroleum Resin is a versatile material with various applications in different industries. Its unique properties make it an essential component in the production of adhesives, rubber products, printing inks, and paints and coatings.
Market Analysis for C 5 Petroleum Resin
Demand and Supply Dynamics
The demand for C 5 petroleum resin is expected to grow at a steady pace in the coming years. The growth in demand can be attributed to the increasing use of C 5 petroleum resin in various applications such as adhesives, coatings, and printing inks. The supply of C 5 petroleum resin is also expected to increase as more manufacturers are entering the market. However, the supply is expected to be constrained by the limited availability of crude oil, which is a key raw material for the production of C 5 petroleum resin.
Price Trends
The price of C 5 petroleum resin is influenced by various factors such as the cost of crude oil, supply and demand dynamics, and production costs. The price of C 5 petroleum resin has been volatile in recent years due to fluctuations in crude oil prices. However, the price is expected to stabilize in the coming years as the market matures and supply and demand dynamics become more balanced.
Regional Market Insights
The demand for C 5 petroleum resin is highest in Asia Pacific, followed by North America and Europe. The growth in demand in Asia Pacific can be attributed to the increasing use of C 5 petroleum resin in the rapidly growing construction and automotive industries in the region. The demand for C 5 petroleum resin in North America and Europe is driven by the growing demand for adhesives and coatings in various end-use industries.
In conclusion, the market for C 5 petroleum resin is expected to grow at a steady pace in the coming years. The demand for C 5 petroleum resin is driven by the increasing use of the product in various applications, while the supply is expected to be constrained by the limited availability of crude oil. The price of C 5 petroleum resin is influenced by various factors and is expected to stabilize in the coming years. The demand for C 5 petroleum resin is highest in Asia Pacific, followed by North America and Europe.
Environmental Impact and Regulations
Emission Controls
C 5 petroleum resin production involves the release of volatile organic compounds (VOCs) into the atmosphere. VOCs contribute to air pollution and can have negative effects on human health and the environment. To minimize the impact of VOC emissions, regulations have been put in place to control the amount of VOCs that can be released into the atmosphere.
Emission controls for C 5 petroleum resin production vary depending on the location and regulations in place. Typically, facilities are required to use emission control devices such as thermal oxidizers or carbon adsorption systems to capture and treat VOC emissions before they are released into the atmosphere.
Waste Management
The production of C 5 petroleum resin generates waste materials that can be harmful to the environment if not managed properly. Waste materials include spent catalysts, contaminated solvents, and other byproducts of the manufacturing process.
To minimize the impact of waste materials on the environment, regulations have been put in place to ensure proper waste management practices are followed. These practices include the use of specialized waste disposal facilities and the implementation of recycling programs to reduce the amount of waste generated.
Overall, the environmental impact of C 5 petroleum resin production can be minimized through the implementation of proper emission controls and waste management practices. Compliance with regulations is essential to ensure that the production of C 5 petroleum resin is conducted in an environmentally responsible manner.
Storage and Handling of C 5 Petroleum Resin
C 5 petroleum resin is a versatile and widely used material in various industries. Proper storage and handling of this resin are crucial to maintain its quality and prevent any hazards. Here are some guidelines for the storage and handling of C 5 petroleum resin:
Storage
- Store C 5 petroleum resin in a cool, dry, and well-ventilated area away from direct sunlight, heat, and sources of ignition.
- Keep the resin containers tightly closed to prevent contamination and evaporation.
- Store the resin in a separate area from other chemicals and materials to avoid any reactions or contamination.
- Do not store C 5 petroleum resin near food, beverages, or pharmaceuticals.
Handling
- Wear appropriate personal protective equipment, such as gloves and safety goggles, when handling C5 petroleum resin.
- Avoid inhaling the resin fumes or dust by using proper ventilation or respiratory protection.
- Do not smoke, eat, or drink while handling the resin.
- Use non-sparking tools and equipment to avoid any ignition sources.
- Do not mix C5 petroleum resin with incompatible materials, such as oxidizers or strong acids.
Following these guidelines will ensure the safe and effective storage and handling of C5 petroleum resin.
Future Trends in C5 Petroleum Resin Technology
As the demand for eco-friendly and high-performance resins continues to grow, the future of C5 petroleum resin technology looks promising. Manufacturers are investing in research and development to enhance the properties of C5 petroleum resins and expand their applications.
One of the key trends in C5 petroleum resin technology is the development of low molecular weight resins. These resins offer improved compatibility with other polymers, resulting in better adhesion, flexibility, and toughness. They are also more cost-effective and have a lower environmental impact than traditional high molecular weight resins.
Another trend is the use of C 5 petroleum resins in hot-melt adhesives. These adhesives are widely used in packaging, woodworking, and automotive industries. C 5 resins offer excellent tack and adhesion properties, as well as good thermal stability and compatibility with other polymers. The demand for hot-melt adhesives is expected to increase, driven by the growth of e-commerce and the need for sustainable packaging solutions.
In addition, C 5 petroleum resins are finding new applications in the construction industry. They are used as binders in asphalt and concrete formulations, providing improved durability, flexibility, and resistance to weathering. With the increasing demand for infrastructure development, the demand for C5 resins in construction is expected to grow.
Overall, the future of C 5 petroleum resin technology looks promising, with manufacturers focusing on developing low molecular weight resins, expanding their applications in hot-melt adhesives and construction, and improving their environmental performance.
Frequently Asked Questions
What are the primary applications of C 5 petroleum resin?
C 5 petroleum resin is widely used as a tackifier in adhesives, hot melt adhesives, and pressure-sensitive adhesives. It is also used as a modifier in printing inks, coatings, and rubber compounds. Additionally, it finds applications in the production of tapes, labels, and other adhesive products.
How is C 5 petroleum resin priced in the market?
The price of C 5 petroleum resin is influenced by various factors, including the demand and supply dynamics, raw material costs, and manufacturing costs. The pricing is typically done on a per-ton basis, and the prices may vary based on the grade, quality, and other specifications.
Where can one purchase C 5 petroleum resin?
C 5 petroleum resin is available from various suppliers and distributors globally. One can purchase it directly from the manufacturers or through authorized distributors. The availability and pricing may vary based on the location and the supplier.
What distinguishes C5 hydrocarbon resin from other resin types?
C 5 hydrocarbon resin is a type of aliphatic hydrocarbon resin that offers excellent compatibility with a wide range of polymers and solvents. It has a low molecular weight and a narrow molecular weight distribution, which makes it ideal for use in adhesives and coatings. Additionally, it has a good balance of properties, including tack, adhesion, and cohesion.
Who are the leading manufacturers of hydrocarbon resins?
There are several leading manufacturers of hydrocarbon resins globally, including Eastman Chemical Company, ExxonMobil Chemical, Kolon Industries, Inc., and Neville Chemical Company, among others. These companies offer a wide range of hydrocarbon resins, including C 5 petroleum resin, C9 petroleum resin, and hydrogenated hydrocarbon resins.
What are the specific uses of C9 petroleum resin?
C9 petroleum resin is a type of aromatic hydrocarbon resin that finds applications in various industries, including adhesives, coatings, and rubber. It is used as a tackifier in hot melt adhesives and pressure-sensitive adhesives, as well as in printing inks and coatings. Additionally, it offers good thermal stability and resistance to UV light, making it suitable for outdoor applications.