Additives Used in Plastics: Understanding Their Purpose and Potential Risks
19/01/2024
Additives are commonly used in plastics to improve their properties, such as durability, flexibility, and resistance to heat and chemicals. These additives can include fillers, stabilizers, plasticizers, and colorants. While they can enhance the performance and appearance of plastics, there are also concerns about their potential impact on human health and the environment.
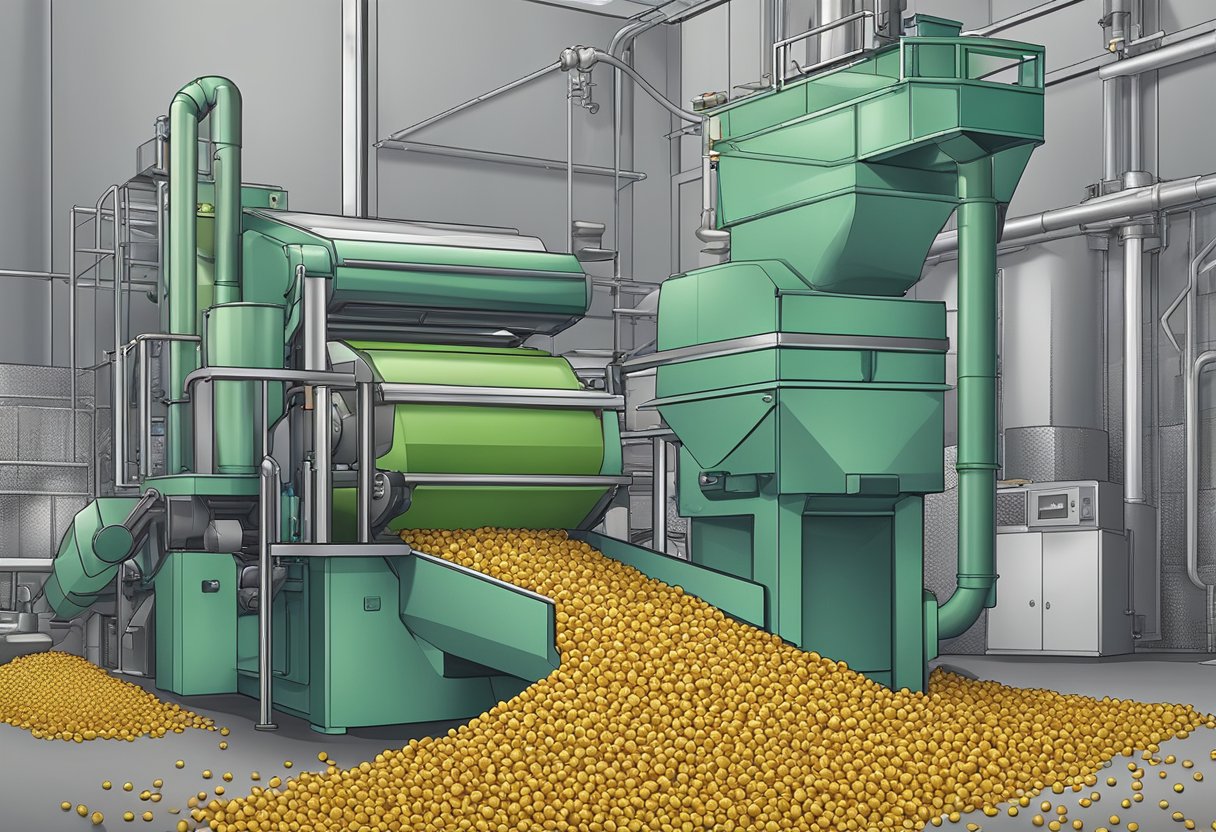
Fillers are often added to plastics to reduce their cost and improve their strength and stiffness. Common fillers include talc, calcium carbonate, and glass fibers. Stabilizers are used to protect plastics from degradation caused by heat, light, and oxygen. Some common stabilizers include antioxidants, UV absorbers, and hindered amine light stabilizers (HALS). Plasticizers are added to increase the flexibility and softness of plastics, and are often found in products such as vinyl flooring and shower curtains. Colorants are used to add color to plastics and can include pigments, dyes, and fluorescent brighteners.
While additives can improve the performance and appearance of plastics, there are concerns about their potential impact on human health and the environment. Some additives have been linked to health issues such as cancer, hormone disruption, and developmental problems. Additionally, additives can leach out of plastics and contaminate the environment, potentially harming wildlife and ecosystems. As such, it is important to carefully consider the use of additives in plastics and to prioritize the development of safer and more sustainable alternatives.
Types of Additives in Plastics
Plastics are made up of a wide range of additives that enhance their properties and performance. These additives can be broadly categorized into four types: fillers, stabilizers, plasticizers, and colorants.
Fillers
Fillers are used to improve the mechanical properties of plastics, such as stiffness, strength, and toughness. They are typically inorganic materials such as glass fibers, carbon fibers, and silica. Fillers can also improve the thermal and electrical conductivity of plastics.
Stabilizers
Stabilizers are used to prevent the degradation of plastics due to exposure to heat, light, and oxygen. They can be divided into two types: thermal stabilizers and UV stabilizers. Thermal stabilizers prevent the breakdown of plastics at high temperatures, while UV stabilizers protect plastics from the harmful effects of UV radiation.
Plasticizers
Plasticizers are used to increase the flexibility and durability of plastics. They are typically organic compounds that are added to the plastic matrix to increase its elasticity and reduce its brittleness. Common plasticizers include phthalates, adipates, and trimellitates.
Colorants
Colorants are used to give plastics their characteristic colors. They can be either organic or inorganic compounds, and are added in small amounts to the plastic matrix. Colorants can also be used to enhance the aesthetic appeal of plastics and make them more attractive to consumers.
Overall, the use of additives in plastics is essential to achieve the desired properties and performance of the final product. The specific types and amounts of additives used will depend on the intended application of the plastic and the desired properties of the final product.
Stabilizers
Stabilizers are a type of additive commonly used in plastics to prevent degradation and maintain their mechanical properties over time. They work by preventing the breakdown of the polymer chains due to exposure to heat, light, or oxygen.
UV Stabilizers
UV stabilizers are a type of stabilizer that protects plastics from the harmful effects of ultraviolet (UV) radiation. UV radiation can cause plastics to become brittle, discolored, and lose their mechanical properties over time. UV stabilizers absorb UV radiation and convert it into heat, reducing the amount of UV radiation that reaches the plastic. Some common types of UV stabilizers include benzophenones, benzotriazoles, and hindered amine light stabilizers (HALS).
Antioxidants
Antioxidants are a type of stabilizer that protects plastics from the harmful effects of oxygen. Oxygen can cause plastics to become brittle, discolored, and lose their mechanical properties over time. Antioxidants work by reacting with the free radicals that are formed during the oxidation process, preventing them from reacting with the polymer chains. Some common types of antioxidants include hindered phenols, phosphites, and thioesters.
Overall, stabilizers are an important class of additives that help to improve the durability and longevity of plastics. By using the right combination of stabilizers, manufacturers can ensure that their products will maintain their mechanical properties and appearance over time, even under harsh environmental conditions.
Plasticizers
Plasticizers are additives used in plastics to improve their flexibility, durability, and overall performance. These compounds are added to the plastic resin during the manufacturing process, and they work by reducing the intermolecular forces between the polymer chains, which makes the plastic more pliable.
Phthalates
Phthalates are a type of plasticizer that has been used in a wide range of plastic products, including toys, food packaging, and medical devices. However, concerns have been raised about the potential health effects of phthalates, particularly their ability to disrupt the endocrine system.
As a result, many countries have restricted the use of certain phthalates in certain applications. For example, in the European Union, the use of six different phthalates is restricted in toys and childcare articles, while in the United States, several phthalates are banned in toys and childcare articles.
Adipates
Adipates are another type of plasticizer that is commonly used in PVC products, such as wires and cables. Unlike phthalates, adipates are not known to have any significant health effects, and they are generally considered to be safe for use in consumer products.
Adipates are also more resistant to high temperatures and UV radiation than phthalates, which makes them a preferred choice for certain applications. However, they are not as effective at improving the flexibility of plastics as phthalates, which means that they are not suitable for all applications.
In summary, plasticizers are an essential component of many plastic products, and they play a critical role in determining their performance and properties. While phthalates have come under scrutiny due to their potential health effects, other plasticizers such as adipates are considered safe and effective alternatives.
Flame Retardants
Flame retardants are additives that are added to plastics to reduce their flammability and prevent them from catching fire easily. They work by either inhibiting or suppressing the combustion process, and are commonly used in products such as electronics, furniture, and building materials.
Brominated Flame Retardants
Brominated flame retardants (BFRs) are a type of flame retardant that contain bromine atoms. They are effective in reducing the flammability of plastics and are commonly used in electronic products such as computers and televisions. However, there is growing concern about the potential health and environmental impacts of BFRs, as they have been found to persist in the environment and accumulate in living organisms.
Chlorinated Flame Retardants
Chlorinated flame retardants (CFRs) are another type of flame retardant that contain chlorine atoms. They are commonly used in products such as furniture and building materials. However, like BFRs, there is concern about the potential health and environmental impacts of CFRs, as they have been found to persist in the environment and have been linked to health problems such as cancer and developmental delays.
Overall, while flame retardants can be effective in reducing the flammability of plastics, their potential health and environmental impacts are a growing concern. As such, there is a need for continued research into the safety and efficacy of these additives, as well as the development of safer alternatives.
Impact Modifiers
Impact modifiers are additives used in plastics to increase their toughness and resistance to impact. They are typically used in applications where the plastic will be subjected to high stress or impact, such as in automotive parts, toys, and packaging.
There are several types of impact modifiers available, including elastomers, core-shell particles, and reactive modifiers. Elastomers are rubber-like materials that are blended with the plastic to improve its impact resistance. Core-shell particles consist of a hard core and a soft shell, which helps to disperse the impact energy and prevent cracks from forming. Reactive modifiers chemically bond with the plastic to increase its strength and toughness.
The choice of impact modifier will depend on the specific application and the properties required of the plastic. For example, if the plastic needs to be transparent, a clear impact modifier may be used to avoid cloudiness. Alternatively, if the plastic needs to be UV-resistant, an impact modifier with UV stabilizers may be used.
Overall, impact modifiers are an important tool for improving the performance of plastics in high-stress applications. By choosing the right impact modifier, manufacturers can create plastics that are more durable, longer-lasting, and better suited to their intended use.
Colorants
Plastics are often dyed with colorants to give them a specific hue. Colorants are added to plastics during the manufacturing process and can be either organic or inorganic pigments.
Organic Pigments
Organic pigments are made from carbon-based molecules and are often used to give plastics bright and vibrant colors. These pigments are often more expensive than inorganic pigments but offer a wider range of colors. Some common organic pigments used in plastics include phthalocyanine blue, quinacridone red, and perylene maroon.
Inorganic Pigments
Inorganic pigments are made from minerals and are often used to give plastics more muted colors. These pigments are less expensive than organic pigments and are often more stable under heat and light. Some common inorganic pigments used in plastics include titanium dioxide, iron oxide, and chromium oxide.
Colorants can be added to plastics in a variety of ways, including through the use of masterbatches, which are pre-dispersed colorants that are added to the plastic during the manufacturing process. The amount of colorant used can vary depending on the desired color and opacity of the plastic. Overall, colorants play an important role in the appearance and functionality of plastics.
Fillers and Reinforcements
Plastics can be reinforced with fillers to improve their mechanical properties. Fillers are materials that are added to plastics to improve their strength, stiffness, and other properties. Reinforcements are materials that are added to plastics to improve their strength and toughness. The most commonly used fillers and reinforcements in plastics are calcium carbonate and glass fibers.
Calcium Carbonate
Calcium carbonate is a common filler used in plastics. It is a white, odorless powder that is added to plastics to increase their stiffness, impact resistance, and dimensional stability. Calcium carbonate is also used to reduce the cost of plastics since it is less expensive than other fillers.
Calcium carbonate is often used in polypropylene and polyethylene plastics. It is typically added in concentrations ranging from 10 to 40 percent by weight. At higher concentrations, calcium carbonate can reduce the impact resistance of plastics. However, it can improve their stiffness and dimensional stability.
Glass Fibers
Glass fibers are a common reinforcement used in plastics. They are made from glass fibers that are woven into a fabric or mat. The glass fibers are then impregnated with a plastic resin to create a composite material. Glass fiber-reinforced plastics are used in a variety of applications, including automotive parts, electrical enclosures, and sporting goods.
Glass fibers are added to plastics to improve their strength and toughness. They can also improve their stiffness and dimensional stability. Glass fibers are typically added in concentrations ranging from 10 to 30 percent by weight. At higher concentrations, glass fibers can make plastics brittle and difficult to process.
In conclusion, fillers and reinforcements play an important role in improving the mechanical properties of plastics. Calcium carbonate and glass fibers are two commonly used fillers and reinforcements in plastics. They are added to plastics to improve their stiffness, impact resistance, and dimensional stability.
Processing Aids
Processing aids are additives used in plastics to improve the processing properties of the material. They are added during the manufacturing process to enhance the flow properties, reduce the processing time, and improve the surface finish of the final product.
There are different types of processing aids available, such as lubricants, release agents, and viscosity modifiers. Lubricants reduce the friction between the polymer molecules, allowing them to flow more easily during processing. Release agents prevent the material from sticking to the processing equipment, reducing downtime and improving efficiency. Viscosity modifiers improve the flow properties of the material, reducing the processing time and improving the surface finish.
Processing aids can be added at different stages of the manufacturing process, such as during compounding, extrusion, or injection molding. The choice of processing aid and the amount added depend on the specific requirements of the final product and the processing conditions.
Some common processing aids used in plastics include:
- Stearates: These are metallic salts of fatty acids that act as lubricants and release agents. They are often used in PVC processing.
- Silicone oils: These are low-viscosity oils that act as lubricants and release agents. They are often used in thermoplastics processing.
- Acrylic processing aids: These are high-molecular-weight polymers that act as viscosity modifiers. They are often used in PVC processing.
Overall, processing aids are essential additives in the plastics industry, as they help improve the processing properties of the material, reducing processing time and improving the final product’s quality.
Antimicrobials
Antimicrobial additives are commonly used in plastics to prevent the growth of bacteria, fungi, and other microorganisms. These additives are particularly useful in products that are used in environments where cleanliness is important, such as hospitals, food processing plants, and laboratories.
There are several types of antimicrobial additives that can be used in plastics, including silver ions, copper ions, and organic compounds. Silver and copper ions work by disrupting the cell membranes of microorganisms, while organic compounds interfere with their metabolic processes.
One advantage of using antimicrobial additives is that they can help to prevent the spread of disease-causing microorganisms. However, it is important to note that they are not a substitute for good hygiene practices and regular cleaning.
It is also worth noting that there are some concerns about the potential environmental impact of antimicrobial additives. Some studies have suggested that these additives may be harmful to aquatic life and may contribute to the development of antibiotic-resistant bacteria.
Overall, while antimicrobial additives can be useful in certain applications, it is important to weigh the potential benefits against any potential risks and to use them in a responsible and informed manner.
Biodegradable Additives
Biodegradable additives are added to plastic materials to allow them to decompose naturally in the environment. These additives are made from natural materials such as cornstarch and vegetable oil, and they help to break down the plastic into smaller pieces that can be consumed by microorganisms.
One common type of biodegradable additive is called oxo-degradable. This additive causes the plastic to break down into smaller pieces when exposed to sunlight or heat. The smaller pieces are then consumed by microorganisms in the environment, leaving behind only water, carbon dioxide, and biomass.
Another type of biodegradable additive is called hydro-biodegradable. This additive causes the plastic to break down when exposed to moisture. The moisture causes the plastic to break down into smaller pieces, which are then consumed by microorganisms in the environment.
Biodegradable additives are often used in plastic bags, food packaging, and other disposable products. While they may seem like a good alternative to traditional plastics, it is important to note that they still contribute to pollution and should be disposed of properly.
Overall, biodegradable additives are a promising solution to the problem of plastic pollution. However, more research is needed to determine their long-term effects on the environment and their effectiveness in reducing plastic waste.
Frequently Asked Questions
What are the typical functions of additives in plastic materials?
Additives are substances added to plastic materials to enhance their properties or provide new ones. They can improve the strength, durability, flexibility, and color of plastics, as well as protect them from UV radiation, heat, and fire.
Which additives are commonly used to enhance the durability of plastics?
The most common additives used to enhance the durability of plastics are antioxidants, which prevent degradation caused by exposure to oxygen and heat, and UV stabilizers, which protect plastics from UV radiation.
How do plasticizers alter the properties of plastic products?
Plasticizers are additives that increase the flexibility and softness of plastic products. They work by reducing the intermolecular forces between the polymer chains, which makes the plastic more pliable and easier to shape.
What role do stabilizers play in the longevity of plastic items?
Stabilizers are additives that prevent the degradation of plastic products caused by exposure to heat, light, and other environmental factors. They work by neutralizing free radicals and other reactive species that can cause chain scission, cross-linking, and other forms of degradation.
Can you list the types of flame retardants used in plastics and their purpose?
The most common types of flame retardants used in plastics are halogenated compounds, such as brominated and chlorinated flame retardants, and phosphorus-based compounds. Their purpose is to prevent or delay the ignition and spread of fire in plastic products.
What impact do UV inhibitors have on the performance of plastics exposed to sunlight?
UV inhibitors are additives that protect plastics from the harmful effects of UV radiation, such as discoloration, embrittlement, and cracking. They work by absorbing or reflecting UV radiation, which prevents it from reaching the polymer chains and causing damage.